FMEA é a sigla em inglês da técnica de Análise de Modos de Falha e Efeitos, o processo de revisar subsistemas, componentes e montagens para identificar possíveis cenários de falha num sistema. Conhecida originalmente como Failure Mode and Effects Analysis, a ferramenta ainda permite buscar pelas causas e efeitos desses modos de falha.
Essa abordagem oferece um paradigma passo a passo para verificar possíveis defeitos num design ou no processo de montagem de um produto ou serviço. Os “modos de falha” são as maneiras como algo pode dar errado. Isso inclui quaisquer defeitos atuais ou em potencial, especialmente aqueles que afetam os clientes.
Já a “análise de efeitos” é o estudo das consequências dessas falhas. Os erros devem ser priorizados de acordo com a gravidade dos seus efeitos, sua frequência e o quão fácil é detectá-los.
Quem faz a avaliação deve documentar o conhecimento atual e os projetos em curso relacionados a falhas e riscos identificados. Isso deve ser usado no processo de melhoria contínua da organização, auxiliando no controle de qualidade antes e depois da operação regular de determinado processo.
Benefícios do FMEA
O FMEA traz diversos benefícios para as organizações que o utilizam, tais como:
- Aumenta a confiabilidade e a segurança dos produtos e processos. Ao identificar as falhas potenciais ou reais, o FMEA permite corrigir ou eliminar as causas dessas falhas, evitando que elas se repitam ou se agravem.
- Reduz os custos e os desperdícios. O FMEA previne ou minimiza os efeitos das falhas, reduzindo os custos e otimizando os recursos.
- Melhora a satisfação dos clientes. O FMEA entrega produtos e serviços de qualidade e confiança, antecipando as necessidades e as expectativas dos clientes.
- Aprimora o planejamento e a gestão de riscos. O FMEA analisa e prioriza as falhas, monitorando e avaliando as ações de melhoria.
- Promove a melhoria contínua. O FMEA documenta e registra as falhas, permitindo que você aprenda com os erros e aplique as melhores práticas.
eBook grátis – FMEA: Um guia completo para identificar e prevenir riscos em sua empresa
Tipos de FMEA
Devido a sua flexibilidade, a Análise de Modos de Falha e Efeitos pode ser usada em diversos contextos, resultando em diferentes tipos de FMEA. A técnica pode ser categorizada de diversas maneiras diferentes, mas geralmente é separada em três grandes classes: DFMEA, PFMEA e SFMEA. Vamos explicar abaixo o que significa cada elemento dessa sopa de letrinhas.
FMEA de Design (DFMEA)
A FMEA de Design (DFMEA) é executada durante a fase de design do produto. O objetivo é melhorar o projeto dessa mercadoria através da descoberta de problemas em potencial.
Para verificar isso, avalia-se:
- Propriedade dos materiais utilizados: lubrificação, viscosidade, elasticidade.
- Geometria do produto: dimensões críticas, interferências, ergonomia.
- Tolerâncias: compatibilidade de montagem, desempenho funcional, durabilidade e vida útil.
- Ruído de engenharia: fontes de ruído, níveis de ruído, impacto no desempenho.
- Demais elementos: segurança, confiabilidade e durabilidade, entre outros.
A DFMEA geralmente é aplicada nas indústrias automotiva e aeroespacial. No caso da automotiva, as montadoras avaliam o design de um novo veículo para encontrar pontos de falha em potencial dentro de componentes críticos. Para isso, elas geralmente verificam freios, motor e transmissão.
Já na indústria aeroespacial, a FMEA de Design é utilizada para analisar o design de uma aeronave com um olho especial para pontos de falha relacionados à segurança e ao desempenho. O objetivo, claro, é resolvê-los ainda durante a fase de design.
FMEA de Processo (PFMEA)
A PFMEA deve ser aplicada durante a manufatura ou a produção de uma mercadoria. Ela determina a busca por falhas que permitam maior confiabilidade e segurança da sua força de trabalho.
Para isso, você precisa avaliar fatores como erros humanos, métodos de análise, materiais e máquinas usadas dentro dos seus processos. Também é recomendado verificar suas métricas de acompanhamento e explorar fatores ambientais.
A PFMEA geralmente é usada em indústrias onde a satisfação dos clientes é um fator crucial, como é o caso da alimentícia. Empresas de alimentos costumam usar essa metodologia de processo para encontrar modos de falha em potencial no seu processo de fabricação.
Esses elementos incluem coisas como contaminação, manuseio inadequado ou problemas na embalagem. Desse modo, dá para identificar os efeitos desses erros na qualidade da comida e na segurança dos consumidores.
FMEA de Sistema (SFMEA)
Por fim, temos a FMEA de Sistema, representada pela sigla SFMEA. Essa é uma análise mais generalizada de falhas sistemáticas. Podemos descrevê-la como uma FMEA de Design só que para o sistema inteiro.
Essa técnica é aplicada durante as fases de serviço ou de manutenção. As etapas para aplicar a SFMEA são basicamente as mesmas da DFMEA, incluindo análises de função, falha e risco.
Os principais setores que utilizam a FMEA de sistema são:
- Indústria de aparelhos médicos: fabricantes de dispositivos médicos e hospitalares usam a SFMEA para encontrar possíveis modos de falha na fabricação ou na operação de seus produtos. O procedimento inclui buscar calibrações incorretas e erros de instalação.
- Indústria de telecomunicações: empresas do ramo de tecnologias da comunicação buscam encontrar falhas nos seus serviços. Aí entram coisas como interrupções de rede, erros de faturamento ou reclamações de clientes.
Para que serve o FMEA?
O FMEA é um método que nos faz pensar: “se essa falha acontecer, quais serão as consequências?” O objetivo é diminuir ao máximo a chance de a falha acontecer, removendo aquilo que a provoca.
Essa ferramenta serve como um resumo de conhecimento, que permite criar um registro baseado em experiências passadas com produtos/processos parecidos e usar essas informações para melhorias futuras.
Usar o FMEA de forma consistente faz com que as falhas sejam evitadas e o serviço fique mais confiável e seguro. Isso traz mais segurança e satisfação para os clientes. Além disso, tem impacto positivo no retorno financeiro da empresa, pois reduz ou elimina possíveis falhas nos processos produtivos.
White paper completo: FMEA – O que é e como implementar na sua empresa
Como aplicar a FMEA
Agora que você já sabe o que é FMEA e quais tipos existem, chegou a hora de aprender como aplicar a técnica na sua organização. É fundamental que a análise seja feita na ordem certa e com um passo de cada vez, pois cada nova etapa depende do resultado da anterior.
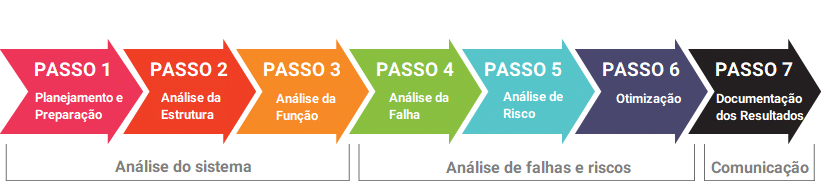
Passo 1: Planejamento e Preparação
O estudo de FMEA começa com uma definição proposital e cuidadosa do escopo. A equipe de gerenciamento é responsável por definir o objetivo do estudo.
Passo 2: Análise da Estrutura
A análise da estrutura é usada para identificar e separar o processo em etapas sequenciais, interfaces e elementos logísticos. Ela usa os limites estipulados pela definição de escopo do passo 1 para identificar cada etapa, interface e elemento logístico do processo que vai ser estudado.
A análise de estrutura tem como objetivo facilitar um entendimento completo do processo. Comece com o elemento central do seu escopo, identifique o processo do qual ele faz parte e aponte todos os elementos que possuem relação direta com ele.
Passo 3: Análise da Função
Na etapa Análise da Função deve ser explorado o que o produto deveria fazer, o que o processo geral (e cada uma de suas atividades) deveria executar e como essa funcionalidade é facilitada. Usando a Análise da Estrutura, desenvolvida no passo 2, cada elemento é analisado separadamente em termos de funções e requisitos correspondentes.
Passo 4: Análise da Falha
No passo 4, o conceito de “cadeia de falhas” é usado para entender e visualizar as imperfeições no processo. Esta cadeia é composta por modo, efeito e causa da falha.
- Modo de falha representa qualquer maneira pela qual um item pode falhar ao atender a função pretendida.
- Efeito de falha é a consequência de um modo de falha.
- Causa de falha é uma indicação do que pode fazer um modo de falha acontecer.
Na análise de falha, você identifica como os elementos detalhados na Análise de Estrutura podem apresentar erros na execução das funções pretendidas — que são documentadas pela Análise da Função. Um modo de falha leva a um efeito acionado por uma causa de falha. A determinação de possíveis causas é o elemento central de uma FMEA.
Passo 5: Análise de Risco
No passo 5, você deve avaliar a gravidade, ocorrência e a capacidade de detecção de cada cadeia de falhas. Com base nas avaliações, determine o nível de prioridade de ação entre “alto, médio ou baixo”.
Use como base as Tabelas de Prioridades de Ação. Vale notar que essas tabelas não estabelecem uma “prioridade de risco”, mas um nível de prioridade para a ação demandada. Com isso, busca-se reduzir o risco de falha no funcionamento.
Se o nível avaliado for alto, obrigatoriamente devem ser tomadas medidas para melhorar os controles de prevenção ou detecção. Caso contrário, ao você deve ao menos justificar o que torna os controles atuais adequados.
Se o nível for médio, é recomendável que medidas sejam tomadas para melhorar os controles de prevenção e ou detecção. Caso seja baixo, ações para melhorar os controles de prevenção ou detecção podem ser tomadas, mas não são obrigatórias.
Passo 6: Otimização
O objetivo principal da etapa de otimização é desenvolver ações para reduzir os riscos e aumentar a satisfação do cliente, melhorando seus processos. A maioria das ações provavelmente envolverá a redução da probabilidade de ocorrência das causas de falha ou a melhoria dos controles de detecção. As duas alternativas levam a um processo mais robusto.
Passo 7: Documentação dos Resultados
Os resultados de cada estudo de FMEA devem ser totalmente documentados.
Um estudo da FMEA não será concluído até que o Passo 7 seja finalizado.
Webinar exclusivo: Identificando e prevenindo riscos com apoio do FMEA
Exemplo de FMEA
A seguir, temos um passo a passo detalhado de como realizar um FMEA. Vale lembrar que este é apenas um exemplo simples e didático para facilitar o entendimento.
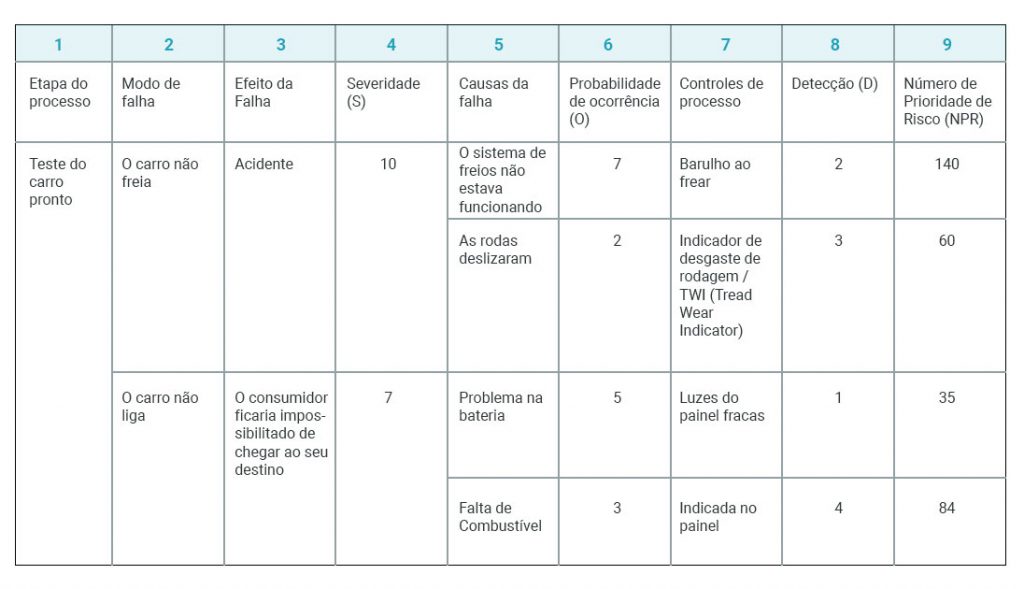
1. Etapa do processo
Vamos considerar o processo de teste de um carro pronto em uma montadora de automóveis.
2. Modo de falha
Neste exemplo de FMEA, definimos dois modos de falha:
- O carro não frear
- O carro não ligar
3. Efeito da falha
Então nos perguntamos: “se essa falha ocorrer, o que poderia acontecer?”. Temos como efeito das falhas:
- Acidente
- O consumidor ficaria impossibilitado de chegar ao seu destino
4. Severidade (S)
Sendo o acidente o pior cenário possível, classificamos o valor de severidade como 10 e para o segundo efeito, não tão grave, classificamos como 7.
5. Causas da falha
“O que poderia causar essas falhas?”. Citamos duas causas prováveis para cada modo de falha:
- O sistema de freios não estar funcionando ou o deslizamento das rodas no teste.
- Problema na bateria ou falta de combustível.
6. Probabilidade de ocorrência
Como se trata de um carro novo e recém-saído da montadora, consideramos:
- Probabilidade de ocorrência 7 (alta) para a probabilidade de o problema estar no sistema de freios e 2 (baixa) de o problema estar nas rodas.
- Probabilidade de ocorrência 5 (moderada) de o problema estar na bateria e 3 (baixa) para a falta de combustível.
7. Controles de processo
Conforme mencionado anteriormente, os controles de processo podem impedir a causa ou detectá-la depois de ter ocorrido. Nesse caso, os indicativos que temos para problemas são:
- Barulhos no sistema de freios. As pastilhas de freio emitem diversos tipos de ruído e cada um deles representa uma falha diferente. Dentre estes temos: squeal de alta e baixa frequência, judder, groan, moan, rattle, clack, chirp e creak. Ou seja, um sistema de freios em pleno funcionamento não apresenta ruídos perceptíveis.
- Outro controle seria o indicador de desgaste de rodagem, o TWI (Tread Wear Indicator). Usamos ele para medir a espessura e profundidade dos sulcos do pneu.
- O painel do carro funciona como controle para detectar tanto o problema na bateria como a falta de combustível.
8. Detecção (D)
Quanto menor o valor da detecção, maior a chance de detectar.
Então classificamos o barulho dos freios como 2 por ser extremamente provável que se escute e 3 para o indicador de desgaste de rodagem.
Já o problema na bateria fica como 1 e a falta de combustível como 4.
9. Número de prioridade de risco (NPR)
Por último, calculamos o NPR. Quanto maior for o valor do NPR, maior é a prioridade daquele item no plano de ações preventivas.
Neste exemplo, o maior número foi o do primeiro modo de falha (o carro não freia), o que quer dizer que a sua verificação deve ser a prioridade de melhoria da montadora.
Resultados do FMEA
Depois de finalizar o FMEA, o que fazer com os resultados?
Esta última etapa é a mais importante, e, caso não seja executada corretamente, todos os passos anteriores serão irrelevantes para o seu produto ou processo.
Após finalizar o FMEA, usamos os resultados para:
- Mitigar falhas de alto risco.
- Reduzir a gravidade das consequências e probabilidade de ocorrências.
- Inserir controles para aumentar a detecção de falhas.
- Criar planos de ação com datas e responsáveis por implementar cada melhoria.
- Reavaliar para garantir que os objetivos sejam alcançados.
SoftExpert FMEA:
Antecipe defeitos com o monitoramento
contínuo do FMEA através de relatórios
e gráficos de risco automáticos
Conclusão
A implementação do FMEA (Failure Mode and Effects Analysis) é um passo fundamental para garantir a qualidade e a segurança de produtos e processos em uma organização. Ao identificar e avaliar os modos de falha em potencial, assim como suas causas e efeitos, as empresas podem agir proativamente para mitigar riscos e aumentar a satisfação dos clientes.
Através das suas diferentes aplicações, como DFMEA, PFMEA e SFMEA, a técnica proporciona uma abordagem sistemática e detalhada para a análise de falhas em diversas fases do ciclo de vida do produto ou serviço.
Assim, o FMEA não só ajuda a identificar problemas antes que eles ocorram, mas também fornece uma base sólida para a melhoria contínua, tornando-se uma ferramenta indispensável para qualquer organização que busca excelência operacional.
Quer conhecer uma solução para melhorar e muito o seu desempenho na elaboração e manutenção dos seus planos de FMEA? Conheça o SoftExpert FMEA.