A CAPA (Corrective and Preventive Action) process is part of the good practices of quality management systems, such as the ISO 9001 and ISO 13485 standards. It is critical to ensure quality and compliance in the manufacturing industry. By proactively identifying the root causes of non-conformities and implementing effective actions, companies reduce rework, operating costs, and regulatory risks.
In addition, a continuous improvement cycle strengthens the quality culture, resulting in greater customer trust and competitive advantage in the market.
Keep reading and see how to put the CAPA process into practice and what benefits this care offers to your company’s operation.
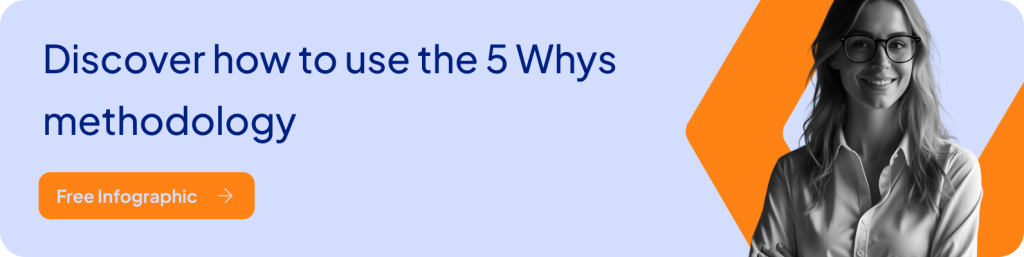
What is CAPA?
CAPA is the acronym for “Corrective and Preventive Action”. These actions are core components of Quality Management Systems (QMS) and are often part of FDA (Food and Drug Administration) guidelines and ISO standards.
One of the most widely accepted definitions of CAPA is in FDA 21 CFR Part 820. According to the agency, it is the process of investigating, analyzing, and eliminating causes of past non-conformities (a process known as “Corrective Actions“) and preventing their recurrence through prospective measures (the “Preventive Actions”).
- Corrective Action: measures to eliminate the cause of a detected non-conformity.
- Preventive Action: initiatives to eliminate potential causes of non-conformities.
Creating, evaluating, and implementing these actions involves a structured flow of activities. Identifying the problem, investigating the root cause, implementing Corrective and preventive Actions, and verifying their effectiveness are common steps in creating CAPA in various industries.
Remember that while Corrective Actions address deviations that have already occurred, restoring the conformity of the process or product, Preventive Actions aim to map risks and implement improvements before failures occur. In this way, it is possible to reduce costs, avoid rework and, above all, eliminate the need for recalls.
The CAPA methodology should result in continuous improvement of the product and the processes involved with it, thus fostering a greater understanding of the mechanisms related to manufacturing. This ensures product safety and efficacy, thus reducing non-conformities.
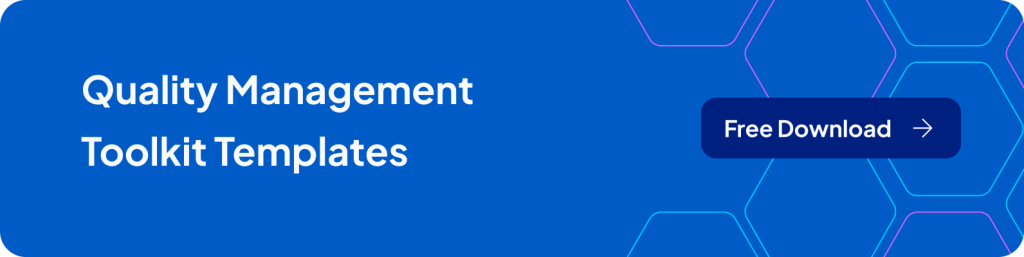
The importance of CAPA in the manufacturing industry
In the manufacturing industry, quality failures can lead to line stoppages, high disposal and rework costs, and regulatory risks that include fines and recall of entire batches.
A well-structured CAPA process allows not only the definitive resolution of recurring problems, but also the identification of opportunities for improvement that increase operational efficiency, reducing cycle times and waste of raw materials.
In addition, the adoption of CAPA strengthens the culture of quality in the factory, encouraging the active participation of employees in identifying deviations and proposing solutions.
This generates an environment oriented to continuous improvement, where performance indicators are monitored in real-time and serve as a basis for internal and external audits, ensuring compliance with regulatory bodies such as the FDA.
Consequently, companies with mature CAPA systems have lower rates of non-conformities, higher customer satisfaction, and a sustainable competitive advantage in the global marketplace.

5 benefits of an efficient CAPA
A well-structured CAPA process brings significant gains to the manufacturing industry, directly impacting product quality, operational efficiency, and competitive advantage.
Companies that adopt corrective and preventive actions maturely record a significant reduction in defects, lower rework and recall costs, in addition to an environment of continuous improvement that strengthens the culture of quality. Below, you will find five of the main benefits that this practice can offer your company.
1. Reduction of non-conformities and rework
A robust CAPA system identifies and eliminates the root cause of deviations, preventing their recurrence and reducing the number of failures in the production process. Therefore, although its implementation requires initial investment, it is soon recovered with the reduction of line stops and recalls. This reduces waste, reduces costs, and avoids downtime periods on the production line.
In addition, by standardizing workflows to address non-conformities, teams gain agility in problem resolution, reducing the average time to close CAPAs.
2. Optimization of operating costs
Each non-conformity implies direct costs (such as disposal of materials and rework) and indirect costs ranging from delays in deliveries to the growth of customer dissatisfaction.
Companies with CAPA integrated into their Non-Destructive Examination NDE reduce these quality-related costs by relying on proactive failure prevention and efficient use of resources.
3. Regulatory compliance and risk mitigation
Regulatory bodies, such as the FDA, require formal CAPA processes for product approval and periodic inspections. The same also applies to certifying bodies (for example, ISO), which require a CAPA structure to grant their certifications.
Therefore, a well-documented and auditable CAPA not only prevents sanctions and recalls but also demonstrates a commitment to safety and effectiveness. This strengthens the trust of customers and partners and solidifies your company’s positive reputation.
In addition, by incorporating risk assessments into the CAPA cycle, companies proactively mitigate potential impacts on the health, environment, and integrity of their product.
4. Continuous improvement and quality culture
A CAPA encourages the active participation of employees, who start to report deviations and suggest improvements with confidence in their management system. The lessons learned, in turn, can be transformed into training, updates to procedures, and key performance indicators (KPI), creating a cycle of improvement.
Having your company CAPA-driven will help you achieve higher levels of internal engagement with respect to compliance and quality. This is because, with this pervasive culture, teams see tangible results from their contributions in reducing defects and increasing efficiency — and thus feel more motivated to continue contributing.
5. Competitive Advantage and Brand Reputation
Companies with a low rate of non-conformities and that have transparent processes gain greater consumer loyalty. In addition, they have easy access to new markets, especially in highly regulated sectors.
The readiness to meet audits and the ability to demonstrate continuous improvements via CAPA are differentials in bids and strategic partnerships. In turn, adherence to them reinforces the company’s position in the global market as a reference in compliance and quality.
In a scenario where compliance and quality dictate purchasing preferences, an efficient CAPA becomes an important marketing and business prospecting asset.
Learn more: what it is and how to make a non-compliance report
The key steps of an efficient CAPA process
1. Identification of non-conformities
The starting point in building a well-structured CAPA is a clear and immediate record of any deviation or potential failure in the production process. These deviations and failures can range from customer complaints to findings in internal and/or external audits.
Some of the typical tools for entering these items include non-conformance reportsHYPERLINK “https://blog.softexpert.com/pt-br/relatorio-nao-conformidade/”, inspection results, and production indicators.
2. Root cause investigation
After identifying the existing deviations and non-conformities, you need to start the systematic analysis of each item to find out why the problem occurred. Some very valuable tools in this process are the 5 Whys method, Ishikawa Diagram (fishbone), and the Failure Mode and Effect Analysis (FMEA).
This phase requires both quantitative and qualitative data collection. That is, you will need to conduct interviews with the employees involved in each process/activity and review procedures. In this way, it is possible to ensure that the real cause of the problem — and not just its symptoms — is identified and treated accurately and quickly.
3. Planning of corrective and preventive actions
Once you’ve identified the root cause of your major non-conformities, it’s time to draw up a well-documented action plan. In it, you should include information with:
- Clear objectives and success metrics;
- Responsible for each task and defined deadlines;
- Necessary resources (training, equipment, raw material changes, etc.);
- Space for reflection or notes after completing a task.
4. Controlled implementation
With your plan approved, it’s time to get it done — but that doesn’t mean it needs to be implemented in any way. Remember to keep records of each step.
Include information such as the start date and evidence of the actions taken. This is essential for traceability. In the case of preventive actions, this record often involves updates of standard operating procedures (SOPs) and training with the teams involved.
5. Verification of effectiveness
After implementation, monitor the indicators relevant to the corrective and preventive actions you have created (such as defect rate, cycle time, number of complaints, among others).
Use this information to confirm that the actions really do eliminate the root cause of the problems and, in addition, do not generate unwanted side effects. In addition, take advantage of any internal audits and periodic reviews to assess adherence to new processes and, thus, find opportunities for adjustments, closing the cycle of continuous improvement.
6. Standardization and lessons learned
Finally, after planning, implementing, and monitoring your CAPA, incorporate the changes into the management system. This may involve updating documents, SOPs, and risk profile matrices, as well as disseminating lessons learned in internal training and workshops.
This way, you ensure that the same type of non-compliance does not happen again and reinforce the culture of continuous improvement in your organization. Then, record the lessons and results achieved and adopt these success patterns in other processes and/or areas of the company.
With these key steps, the CAPA process is no longer just a regulatory requirement and becomes an engine of operational excellence. Armed with this strategy, you can reduce failures, costs, and risks, and at the same time increase team engagement with compliance measures and, consequently, customer satisfaction with higher quality products.
How SoftExpert can help your company build a CAPA
SoftExpert offers a complete solution to support your entire CAPA journey — from capturing non-conformance to standardizing lessons learned. With our solution, you can integrate task automation, cause analysis, real-time monitoring of indicators, and even count on specialized support.
With specific modules and configurable workflows, SoftExpert Suite ensures not only compliance with the regulatory requirements of the manufacturing industry but also effectiveness and agility in problem solving, promoting continuous improvement and the reduction of non-conformities in production.
Automated workflow and non-conformance management
- SoftExpert’s Enterprise Quality Management (EQM) centralizes the registration of non-conformities and automates the entire CAPA cycle, from case opening to closing.
- Notifications and approvals are triggered automatically, reducing delays and ensuring complete traceability at every stage of the process.
- SOPs, audit reports, and evidence are linked to CAPA within the tool, avoiding loss of information and facilitating internal and external audits.
Advanced root cause analysis tools
- To support systematic research, the platform offers established visuals and methodologies such as Ishikawa Diagram, 5 Whys, and FMEA integration.
Monitoring indicators and verification of effectiveness
- You can view real-time dashboards to keep track of critical CAPA metrics.
- It is possible to define configurable KPIs, such as CAPA reopening rate, average closing time, associated costs, and many others, which can be viewed by area or project.
- The platform allows you to create proactive alerts. This way, you have notifications about missed deadlines and performance deviations, which prevents corrective actions from losing effectiveness.
Integration with other solutions and mobility
- The platform is modular and fully integrated, providing a unified view of your company’s quality processes.
- The system brings connection between ERP, CRM and your company’s legacy systems. This ensures data consistency and eliminates rework from manual entries.
- Shop floor teams can record non-conformities and attach photos directly from their smartphone or tablet, speeding up the CAPA cycle and speeding up action — which in turn reduces the negative impacts of non-conformances.
Consulting, training and support services
In addition to technology, SoftExpert offers services to maximize the benefits that the platform offers your company:
- Specialized consulting with process mapping, definition of indicators and structuring of CAPA flows according to the sector’s best practices and adapted to your company’s reality.
- Training and continuous training workshops for employees on the best use of the platform and how to create a culture of quality and constant improvement.
- Global support with offices and partners in more than 50 countries to ensure local and personalized service to your company’s regional regulatory requirements.
With SoftExpert Suite, manufacturing industries have a robust and modular solution to build truly efficient CAPA processes, reducing non-conformities, costs and risks, while strengthening their culture of operational excellence.
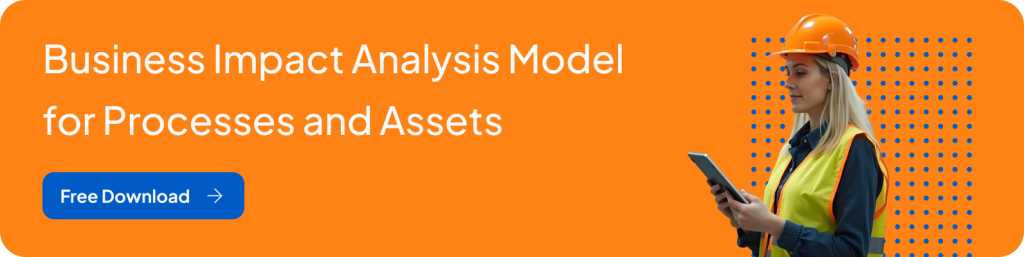
Conclusion
Implementing and maintaining an efficient CAPA process is key to reducing non-conformities in the manufacturing industry. With the right tools and a culture of continuous improvement, companies become more competitive, reduce operating costs, and increase customer satisfaction.
Looking for more efficiency and compliance in your operations? Our experts can help identify the best strategies for your company with SoftExpert solutions. Contact us today!