The 5S methodology, also known as the 5S program, is a technique for organizing and cleaning the workspace to achieve greater efficiency and effectiveness. Of Japanese origin, she advocates for identifying the most frequently used items to separate them from the less important, classifying them in a way that optimizes productivity. To this end, the methodology relies on five principles: Seiri (utilization), Seiton (organization), Seiso (cleanliness), Seiketsu (normalization), and Shitsuke (discipline).
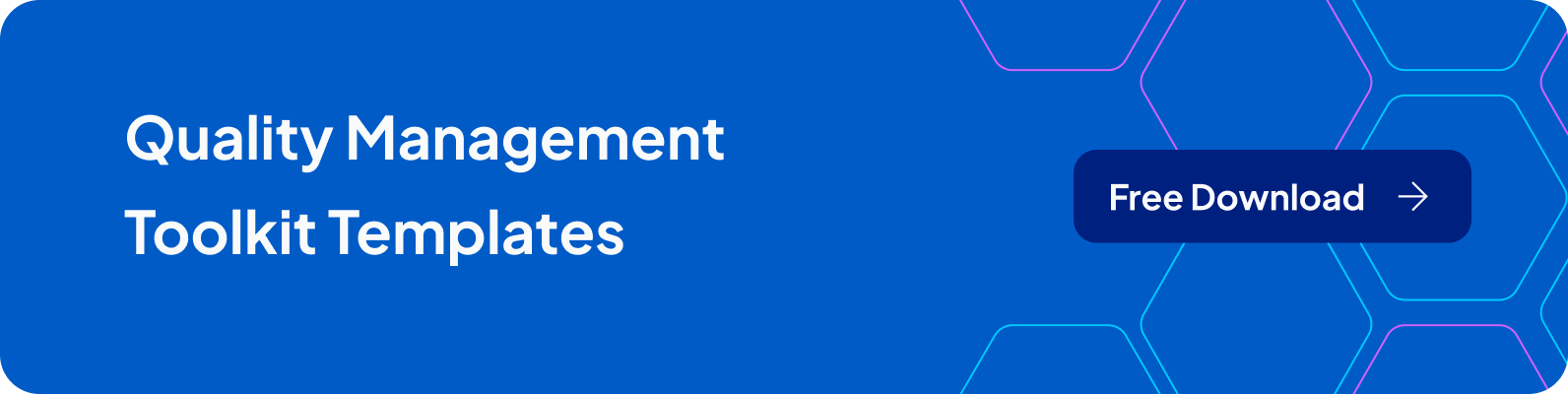
What is the 5S methodology and how did it come about?
The 5S program got its start in the 1970s with the Toyota Motor Company in Japan. Supported by the five pillars of execution, the 5s methodology allows you to organize various sectors of a company based on the production, standardization, and cleaning necessary in that environment. This ensures that it is conducive to the activities and, in this way, generates better results.
At the time of the creation of this technique, the leaders of the Toyota Motor Company sought to reduce manufacturing waste and inefficiencies. For this, the 5S methodology emerged: a system that would allow “Just in Time” manufacturing.
It was then that the five pillars were established for the concept of the visual workplace. Over time, this idea was popularized in the 5S methodology as we know it today.
The goal of the 5S program is to make the workplace better by standardizing processes to increase efficiency, employee satisfaction, and the productivity of the organization. Since its inception, the 5S methodology has sought to create a culture of discipline to identify problems and generate opportunities for improvement.
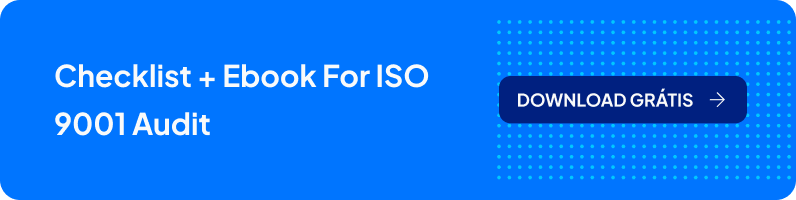
What are the five principles of the 5s methodology?
The principles of the 5S methodology were developed in Japan in the 1970s and are based on five Japanese vocabulary words:
- Seiri (Sense of use);
- Seiton (Sense of organization);
- Seisou (Sense of cleanliness);
- Seiketsu (Sense of standardization);
- Shitsuke (Self-Discipline Sense).
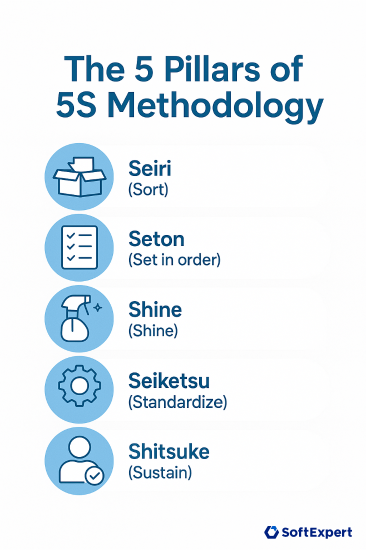
The principle of these pillars is to keep the work environment clean, organized, safe, and tidy. In addition to the benefits for performance, the technique also promises waste reduction. This all contributes to the creation of a good quality work environment, both from a physical and mental perspective.
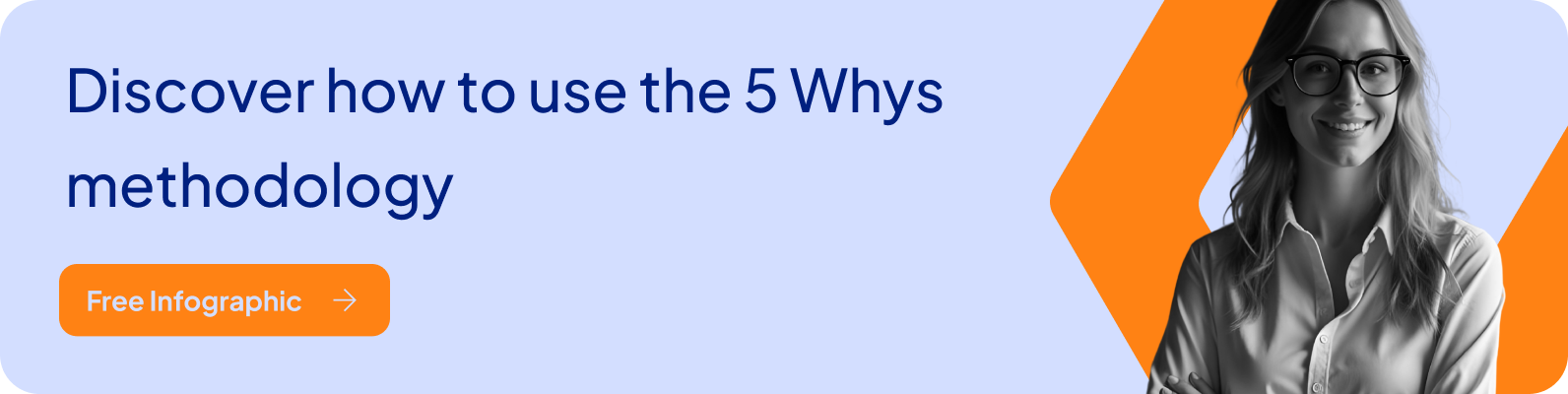
Advantages of using the 5S
Even though it was developed for the automotive market, the 5S methodology is widely used in many different industries. This is due to its flexibility, its low investment cost, and the great impact it has on the organizations where it is implemented.
Learn about all the advantages of implementing the 5S program in your company:
- Increased productivity. By making your work environment more organized and efficient, you improve the morale and productivity of your employees.
- Better security. The Seiri step reduces the risk of accidents such as trips and falls, while the Seiton minimizes the chance of injuries caused by improperly stored tools.
- Increase the quality of your products. With the standardization phase, you can reduce variability in manufacturing, leading to more consistent and higher-quality production.
- Cost reduction. Your business can reduce storage expenses and maintain optimal inventory levels. The 5S methodology also increases the durability of your equipment and decreases repair expenses.
- Improved work environment. Not only do you make your environment more organized and cleaner, but you also limit how far your employees have to walk to perform their duties.
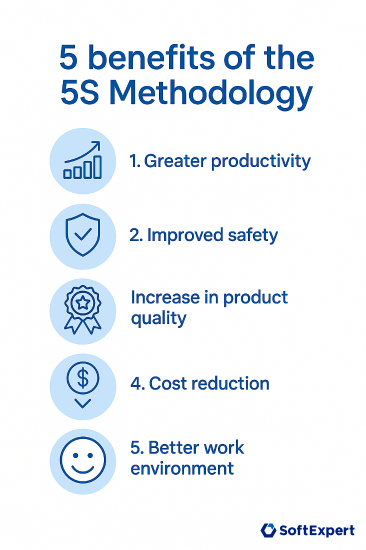
In addition to all these items, the 5S program also puts your organization on the right path to implement continuous improvement. As the icing on the cake, the technique also increases stakeholder confidence in your company by offering greater transparency, engagement, and long-term customer satisfaction.
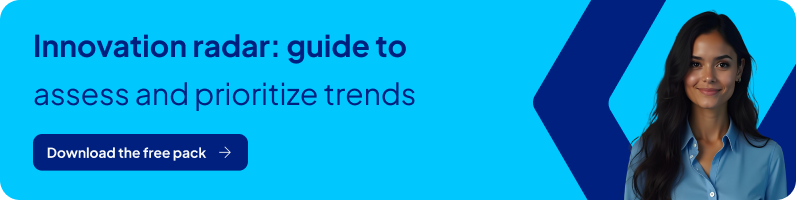
How to apply the 5S methodology in your organization
We already understand the origin and purpose of the technique. The entire team is already trained, and the top management is engaged. So, how to start the program? Below, with the explanation of each of the five pillars, we will detail the steps that can be followed by your organization to start implementing this tool.
Seiri (Sense of use)
This first step is responsible for separating what you use from what you don’t. What you don’t use can get in the way and take up space. And of course, space is money, no matter what your organization does.
Start in a simple way: ask how your computer desktop is doing. Is it organized and only with the documents and programs you use frequently, or is it full of items that are no longer used?
Going further, let’s go to your work environment. Develop criteria for the disposal of items not needed and, together with your colleagues, identify items used and not used in everyday life.
A tip: always take photos of how your desktop looked before making changes. People’s reaction to observing the before and after is fantastic!
List a place for disposal, donations, or even sale of unused items in your company. Set a general day when the entire company will mobilize to carry out the initiative.
Seiton (Sense of Organization)
Look at the items that have been chosen as necessary to separate and organize them. Decide where to put each thing, always considering the flow of your work.
If the item is used very often, leave it close to you or where it is used. If it is used a little less frequently, store it in a closet, for example.
Still, it is important that he is close to you and that the consultation can be done quickly. An example of such an item would be a document that you refer to once a week.
Items that you use even more frequently can be stored in closets or in more distant places, without the need for immediate and quick access.
Seiso (Sense of cleanliness)
The time has come to clean. A dirty environment prevents you from finding opportunities for improvement. Therefore, ensure that your work environment is clean and that anomalies can be found.
Adopt cleaning as a daily activity and part of an inspection. Clean your workplace before you start your shift and before you finish it.
Seiketsu (Sense of standardization)
This step is responsible for creating visual controls and guidelines to keep the workplace organized, orderly, and clean. Before starting this phase, make sure that all the previous steps have been carried out correctly.
Create procedures and forms to regularly assess the status of the first three principles.
Generally, each employee is assigned some specific function that contributes to the cleanliness of the environment. Scheduled routines are defined with weekly, biweekly, or monthly periodicities. Supervisors are responsible for keeping track of tasks that are being performed.
Shitsuke (Self-Discipline Senso)
This step involves discipline to ensure that all employees follow the standards of the 5S program. They should practice the first four Senses spontaneously and voluntarily, basically as a way of life. In this way, 5S becomes an integral tool of the organization’s culture.
Each of the senses must have an audit associated with it, where it will be verified if each of the points implemented is maintained.
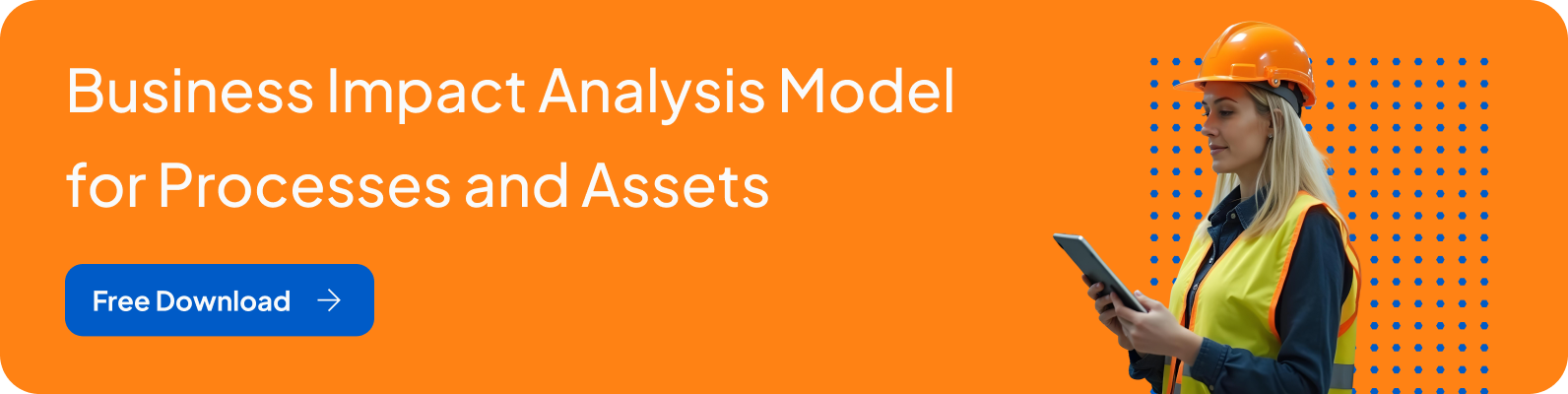
How the 5s methodology works
The 5S methodology is cyclical, starting with the use of items and ending with the standardization of processes. The order to be followed is as follows: use, organize, clean, and standardize.
Throughout the process, it is necessary to maintain a sense of self-discipline. All of this allows the technique to result in continuous improvement for your organization. See a brief step-by-step guide on how to implement the 5s methodology in your company.
- Seiri (sense of use): Focus on eliminating unnecessary items from your workplace. To do this, you need to remove from your professional environment any element that is not used in your current operations.
- Seiton (Sense of organization): Have your team keep the necessary items in the correct place, so that they are easily used.
- Seisou (Sense of cleanliness: Start as soon as most of the clutter has been removed. This is the time when you do a thorough cleaning of your desktop.
- Seiketsu (Sense of Standardization): Once the first three steps have been implemented, it’s time to standardize these best practices on the desktop.
- Shitsuke (Sense of self-discipline): Maintain this philosophy throughout the execution of the methodology. Without maintaining this cycle of continuous improvement, the changes in the other pillars will not last long.
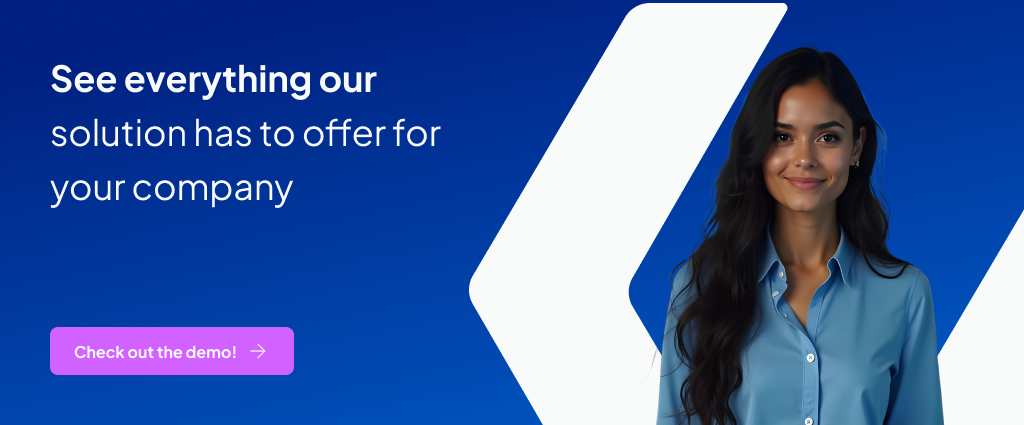
Conclusion
The implementation of the 5S methodology can significantly transform the work environment, promoting greater organization, cleanliness, safety, and efficiency.
Adopting this technique is not just a matter of improving the physical appearance of the workplace, but rather of creating a culture of discipline and continuous improvement that benefits all levels of the organization.
By following the five senses — Seiri, Seiton, Seisou, Seiketsu, and Shitsuke — your company will take important steps toward a more productive and enjoyable work environment.
The benefits go beyond productivity and waste reduction: they include improved product quality, employee safety, and stakeholder satisfaction.
With careful implementation and upholding the principles of the 5S methodology, your company will be able to experience a true transformation, laying a solid foundation for continued innovation and growth.
Therefore, if you are looking for a way to optimize processes, engage employees, and achieve operational excellence, the 5S program is a powerful tool that can make all the difference. Invest time and resources in its application and reap the rewards of a more efficient and harmonious work environment.
Looking for more efficiency and compliance in your operations? Our experts can help identify the best strategies for your company with SoftExpert solutions. Contact us today!
FAQ
It is a Japanese technique for organizing and cleaning the workspace, composed of five senses, which seeks to increase efficiency, effectiveness, and productivity.
It was created in the 1970s by the Toyota Motor Company in Japan to reduce waste and inefficiencies and enable the “Just in Time” manufacturing system.
Standardizing processes, organizing and cleaning the environment, increasing efficiency, employee satisfaction, product quality, and fostering a culture of discipline and continuous improvement.
1. Seiri (Utilization);
2. Seiton (Organization);
3. Seiso (Cleaning);
4. Seiketsu (Standardization);
5. Shitsuke (Self-discipline).
• Seiri: Separating used items from unused ones and discarding or disposing of the latter.
• Seiton: Logically arrange necessary items according to the frequency of use.
• Seiso: institute daily cleaning and inspection to identify anomalies.
• Seiketsu: create visual controls, procedures, and forms to maintain the correct application of the previous senses.
• Shitsuke: Develop discipline so that everyone practices the four senses as a daily habit.
• Increased productivity and team morale;
• Improved safety and reduced accidents;
• Increased product quality and consistency;
• Reduction in inventory and maintenance costs;
• A more pleasant and organized work environment;
• Stakeholder engagement and culture of continuous improvement.
1. List and sort used and unused items (on your computer and in the physical environment).
2. Define disposal criteria, donation/sale points, and schedule a joint effort for removal.
3. Position everyday items close to the point of work.
4. Store items of weekly use in nearby lockers.
5. Accommodate items of sporadic use in less accessible but still organized locations.
6. Include cleaning as part of the daily inspection routine to detect faults.
7. Create procedures, checklists, and forms to evaluate the application of the first three senses.
8. Assign responsibilities and periodicities (weekly, biweekly, monthly) to the check-in tasks.
9. Conduct regular audits in each sense.
10. Embed the 5S program into the organization’s culture as a way of life.
Due to its flexibility, low implementation cost and high impact on organization, safety, quality, and culture of improvement, this philosophy can be applied in any type of industry, size of organization, and sector of the company.